The path to net-zero includes sustainable materials and building performance standards
The construction of sustainable, net-zero buildings will play a significant role in helping Canada reach its goal of net-zero emissions by 2050. The use of materials such as mass timber reduces carbon emissions as well as allows buildings to be constructed faster, with lower labour costs and less waste. Incorporating new building performance standards such as LEED and Passive House also ensure new buildings are as energy efficient as possible.
During a recent ReNew Canada Webinar—with support from PCL Construction—a panel of experts discussed how Canada’s educational institutions are leading the charge on sustainable construction and helping to take some of the risk out of new building techniques.
ReNew Canada: Why are so many educational institutions leading the way when it comes to the use of sustainable construction methods and building materials?
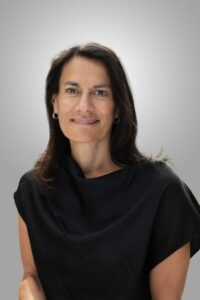
Nerys Rau (Geroge Brown College): I think educational institutions have different decision-making drivers than many sectors, particularly the private sector. And this is I think why we’re uniquely positioned to drive change and be willing to drive change. With Limberlost Place we really wanted to be an example of change, demonstrate innovation, and refute the misconceptions about sustainability; that it’s possibly too expensive, for instance. It is also a living lab for us and for our students. We’ve also been extremely open about building in general, having done more than 125 tours. We’ve opened it to consultants, architects, engineers, contractors, developers, other public institutions who have come through the building and we’ve talked to them about the methodologies, the vision, our challenges, which are really important to us to drive change with this building.
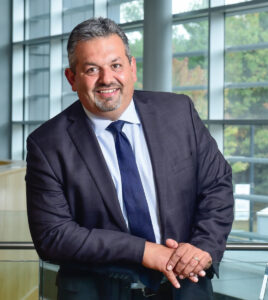
Andrew Arifuzzaman (University of Toronto Scarborough Campus): Students are making choices about where they want to go to school. They want to go to institutions that reflect the values that they’re bringing forward. And so that’s I think part of it. I think the other reason that the post-secondary sector has such an opportunity around driving innovation is because we build probably the most diverse building stock out there. It’s everything from a student residence, a high-tech science building, warehouse buildings, athletic centres, office buildings. And there’s not a lot of other sectors that build that kind of diversity.
And each one of those building types lends itself to different forms of innovations. It really allows us to push boundaries in a way that other sectors don’t. And given that we’re building buildings for the long term, we can take on some of that risk. We’re bringing expertise, working with some of the best consultancy groups in the world on driving this kind of innovation. And then de-risking the marketplace for future projects.
ReNew Canada: How are building standards and regulations helping to meet the challenges of sustainable construction?
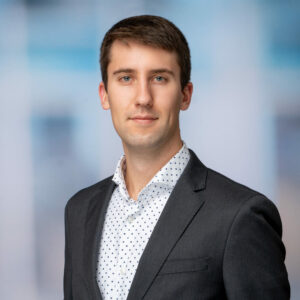
Ryan Going (Pomerleau): I think standards and regulations play a huge part in driving the industry forward. LEED, I think, is less applicable now than when it debuted. For example, when LEED first started to come out, no contractors with very few exceptions were separating their waste, and now it’s standard practice. Today LEED has been somewhat eclipsed by new standards, such as Passive House, that are really pushing the boundaries on the next generation of sustainable buildings. And it’s not just the industry that needs to understand these new standards, but also the authorities that are issuing the building permits as well. It’s a challenge we’ve encountered on our University of Toronto Academic Tower project, specifically regarding the use of mass timber. There is still a lot of misunderstanding when it comes to the building material, thinking that it’s a huge fire risk. We had to add a secondary redundant fire line to the project, which is not a normal requirement. It’s just one example of where the permitting regulations haven’t caught up to the industry.
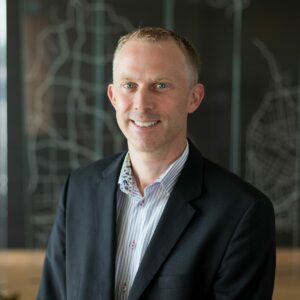
Mark Henderson (PCL Construction): Without codes in place, all we really have are standards that are driving us to the next levels. We’re anticipating an energy code release in 2030, but between now and then, a lot of time is going to be spent marching towards the goal of net-zero. And many of the standards deal with energy efficiency and anytime we can incorporate these standards to raise awareness of what we’re doing is important. We all love getting plaques on our buildings and the accolades that go along and awards but having that educational awareness I think raises the bar as well. All these standards have very rigorous performance verifications that need to be done. In the case of the Passive House renewal of the Ken Soble Tower we did for the City of Hamilton, there was a lot that went into understanding the performance and verification to achieve certification.
ReNew Canada: What are the advantages and challenges of including sustainable construction materials, such as mass timber, in your projects?
Nerys Rau: I think the holistic advantages are obvious. We can’t continue to rely on non-renewable resources. We have to reduce the overall carbon footprint of production of construction in general and we must reduce the amount of waste that’s created during construction. Sustainable construction has three pillars, social, economic, and environmental, whereas more traditional construction speaks to economy, utility, durability. And that’s an important distinction. To me, that means that through sustainable construction, socially, we’re trying to enhance people’s quality of life. And from an environmental perspective, we’re trying to minimize the adverse effects of construction because we’re going to continue to build buildings, but how can we do that in an effective way? Upfront planning is essential for success on these projects. You need to engage with local authorities, so they understand what your vision for the building is going to be. And don’t assume their knowledge. Don’t assume that just because there’s the presence of some champions within those authorities that that’s going to ease your way. It’s still a challenge because with these materials, we’re building outside the code. With Limberlost, it’s a tremendous number of alternative solutions that have got us to where we are and that’s still a lot of work.
Mark Henderson: One of the advantages when it comes to using mass-timber is that you can generally fabricate lighter buildings, which means smaller footings and smaller foundations. And with that comes less embodied carbon, which I think is the ultimate goal. There is a learning curve certainly with how these buildings get put together, but with proper collaboration and communication those challenges can be overcome. Availability is also a challenge when it comes to mass timber, so mapping out the supply chain is key. Who’s got capacity, who doesn’t? I think mass timber will have longevity, but there’s not a lot of producers in Canada and North America that have the capacity to meet the demand. Similarly, on the labour side, there’s not a lot of trades that understand how to assemble these wood buildings.
Andrew Arifuzzaman: The supply chain is a huge issue for us, not only for mass-timber. For our Passive House project, we brought in triple glaze thermal windows and there were no local suppliers. Some windows came in from Germany, and some windows came in from Colorado that could meet the kind of standard that we needed for that project. Part of the hope in doing these projects is that as industry evolves, as developers begin to come into spaces like Passive House, it creates demand. We also had to work with our partners to train our local workforce on how to install the windows. Often we’re working with consultancies, engineers, architects who are new to this space and they’re figuring this out as we go. You really need to assemble a solid team that can take products and install them correctly.
With such a tight supply chain in the mass timber market, sometimes the right thing to do is to not do the thing that you thought you were going to do, so that others can step up and achieve what their objectives are. We had a 450,000 square foot mass-timber parking garage that we were looking at building, that ultimately would have tied up a mass timber producer and put them out of circulation for everybody else. To reflect that market reality, they priced themselves accordingly. And so, the project value wasn’t there any longer for us.
Ryan Going: When you’re using sustainable materials on any project and you’re at the forefront of the cutting edge of these technologies, one of the biggest advantages is the opportunity to be at the front of that learning curve. But it’s also a challenge, because we’re finding out what all the problems are as you go. I think one of the biggest barriers to sustainable construction is that lack of knowledge in the industry. The fact is 99 per cent of the industry are still not familiar with these types of projects and these materials and systems. That’s a challenge, but it’s also an opportunity because from our perspective, if we want to be leading the industry and be the contractor of choice for these types of projects as they become more common, we need to be leading the industry now and taking on these challenges. But with that opportunity I think also comes a responsibility, which is to take those lessons learned and collaborate and share them and help educate the industry.
John Tenpenny is the editor or ReNew Canada.
[This article originally appeared in the November/December 2023 edition of ReNew Canada]
Featured image: George Brown College’s low-carbon, net-zero Limberlost Place is already considered a new global model for mass timber construction. (Salina Kassam)