By Elena Theodoropoulos
Historically, the construction industry has been slow to adapt to digital change and innovation. This is despite demand for infrastructure skyrocketing due to government stimulus such as the $1.2-trillion Bipartisan Infrastructure Law in the U.S. and the $180-billion Investing in Canada Plan in Canada. The strong demand for infrastructure is being curbed by a shortage of skilled labour. Technological innovations known in the construction sector as ‘con-tech’ can help deliver infrastructure more efficiently.
Con-tech can be used in all parts of the construction lifecycle—from the design and planning stage, throughout the actual construction and into the operations and maintenance phase. These innovations include design software, robotics and tools to make scheduling or budgeting more efficient and tools to monitor construction site progress and safety.
Ontario’s recent $5-million investment in digital twin technology marks a significant step forward in the evolution of using con-tech in Canadian public infrastructure projects. By integrating digital twin technology, Ontario is stepping into a transformation in infrastructure project management, with far-reaching benefits for risk mitigation. This investment has the potential not only to save time and money, but also increase the ability to assess and mitigate risks, leading to other results such as improved safety conditions for workers on site.
The increasing use of digital twin technologies for public infrastructure projects is already changing how Canada’s insurance industry approaches the construction sector. Insurers are increasingly recognizing the value of con-tech like digital twins in reducing risk. Some insurers are offering lower premiums for projects that use this technology—and in some cases even subsidizing its implementation. Digital twin technologies are an all-around win for project owners, contractors, governments, taxpayers and, yes, insurance companies.
Understanding digital twin technology
Digital twin technology creates a detailed virtual replica of a physical asset, system or process. This digital model is continuously updated with real-time data from multiple sources, which allows for a dynamic and accurate representation and the ability to test out multiple ‘what-if’ scenarios and simulations of different risks.
Essentially, it creates a virtual model that is the exact counterpart of a physical thing. The idea of using a digital twin likely originated with NASA in the 1960s when the organization replicated a version of their spacecrafts on Earth for study and simulation purposes. You may be familiar with the term Building Information Modelling (BIM)—A digital twin is similar to BIM in that both can model a project and allow many parties to collaborate. However, a digital twin can have a real-time operational response. Due to the complexity of building a digital twin, they are usually geared towards complex sectors. Therefore, the construction industry is the perfect fit for this technology, due to the complex nature of projects and assets being built and operated. When applied to construction projects, digital twins can map every aspect of a project, from initial design and planning to construction through operation and maintenance.
Digital twins are particularly helpful for assets with complex systems such as plumbing, mechanical and electrical operations within structures. In fact, the province of Ontario has selected Peter Gilgan Mississauga Hospital and the Ontario Place Rebuild to test digital modeling technology due to their complex utility systems. Digital twins have the ability to identify and map utilities, with the aim to avoid utility conflicts that can end up being extremely costly and cause project delays.
The ability to visualize and interact with a digital replica is a powerful tool for risk mitigation, making it easier to predict, prevent and manage risks that could otherwise lead to costly delays, accidents or failures.
Benefits of digital twins in construction
One of the most significant advantages of digital twin technology is its ability to provide real-time monitoring for infrastructure projects. Sensors embedded in and around a structure feed data into the digital twin. For example, if part of a structure shows signs of stress or water damage, the digital twin can alert the project team so they can address the issue before it becomes a major problem. A digital twin can benefit all phases of a project. During the planning phase, digital twins enable simulations of various scenarios, which drives better decision-making. Before any physical work begins, the digital twin can model different construction approaches, material choices and even environmental factors. By evaluating these scenarios virtually, project managers or designers can make informed decisions that minimize risks.
For example, if a city was planning a new rail line connecting their airport to the city or a new highway route, a digital twin could be used to analyze different route options through a 3D model with collaboration from all stakeholders. This allows for more accurate and efficient planning, and ultimately helps determine the most efficient route. During the construction phase, as work progresses, it can be monitored against the ‘as-designed’ version of the asset, ensuring that construction is progressing as it should be.
Digital twins enhance worker safety on site. By simulating the construction process in a virtual environment, potential safety hazards can be identified and mitigated before they pose a risk to the actual site. Using other technologies that feed data into the digital twin (i.e. 360-degree video) can also provide a detailed snapshot of the site, allowing for the remote identification of issues before they have the chance to become costly mistakes.
By providing a detailed, real-time view of the construction process, digital twins can also help ensure that a project meets regulatory requirements. This reduces the chance of costly delays or fines due to non-compliance. On top of that, digital twins enable better documentation and reporting, which can also help ensure that projects stay on track.
In the operational phase, a good example of using a digital twin for operations is the insurance company Swiss Re, who are monitoring a ship sailing from Asia to Italy using digital twin technology. The twin takes data from the systems of the ship—if the twin signals that the ships engine requires maintenance, the captain can then stop for a repair, thus avoiding a machinery breakdown insurance claim from occurring (which average at $600,000 per claim). This ends up saving both the insurer and ship owner time and money. This same principal can be applied to specific buildings, general infrastructure, and other assets once completed. For example, the sensors in a building can be used to detect water infiltration, which can allow for prevention before more of the building is damaged.
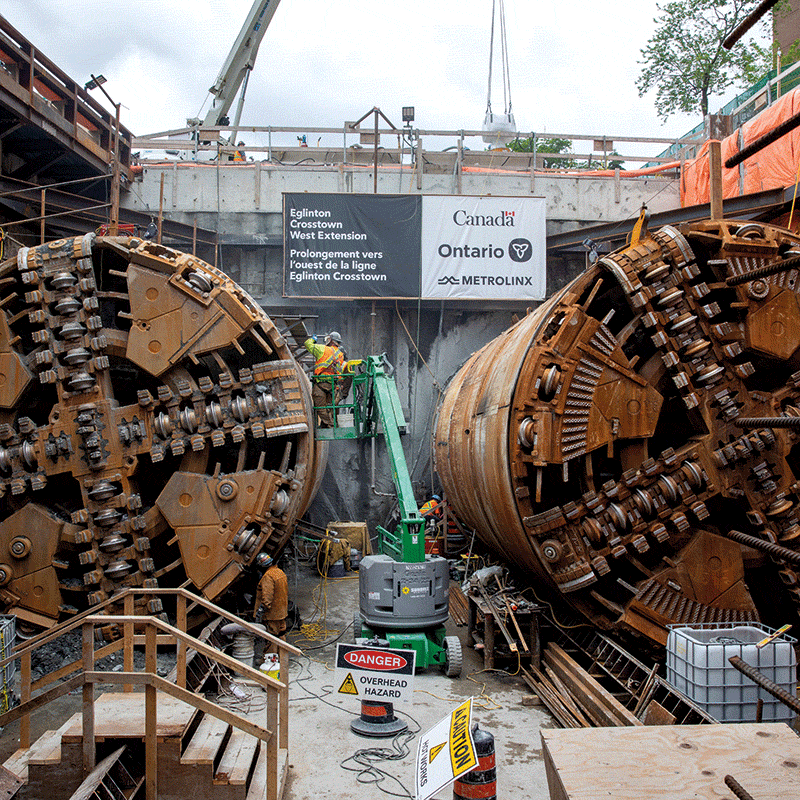
Lower insurance premiums and faster claims
Integrating digital twin technology in public infrastructure projects also has significant implications for the insurance industry, particularly in construction. Insurance costs have increased around 25 per cent each year for the past four years globally. The cost of insurance as a percentage of project value is around 3.5 per cent in Canada and can be up to 10.4 per cent in certain states such as New York. The ability to use risk controls such as a digital twin can mitigate premium spend. While insurers traditionally have and still rely on historical data when assessing a project, digital twin technology allows for a more sophisticated approach to risk analysis and underwriting. It gives insurers the ability to visualize the project and analyze various ‘what-if’ scenarios—such as the impact of a flood or fire on the project site—and see the effect of risk mitigation techniques.
Digital twins provide a wealth of data that enables more accurate risk assessment. Knowing that the project will have real-time data about important risk factors makes insurers more confident that these risks will be identified and mitigated before losses occur. It allows them not only to better understand the risks associated with a particular project and tailor coverage accordingly—it gives them reassurance that there is greater risk mitigation built into the project than there would be without digital twin technology. This precision in risk assessment leads to more tailored pricing of insurance policies, often lowering premiums for project owners and contractors.
Over time, the data generated by digital twins will also improve the underwriting process. Insurers can use this data to develop more sophisticated models for assessing construction risks, leading to better-informed decisions about coverage. When incidents happen, the data from the digital twin can also make the claim process easier for insurers and clients alike. By providing a detailed and accurate record of the construction process and the structure itself, digital twins enable faster claims processing, giving all parties to a claim (insurer, broker, client and loss adjuster) the ability to exchange information quickly. The digital twin can also facilitate the faster repair of a damaged asset.
Saving taxpayers money
Using digital twin technology in public infrastructure projects has significant benefits for taxpayers, who ultimately bear the cost of these projects. Digital twins offer real-time risk mitigation and reduce the likelihood of costly errors or delays.
The main way digital twins save money is by reducing construction cost overruns. By finding and addressing potential issues early in the project lifecycle, digital twins minimize the need for costly rework or modifications during construction. This should lead to more projects being completed on time and under budget, reducing the financial burden on taxpayers.
Digital twins also enhance transparency and accountability in public infrastructure projects. By providing a detailed, real-time view of the project’s progress, digital twins enable better oversight and reporting. This transparency helps ensure that public funds are spent appropriately and that the project benefits the community as intended.
When construction is done, digital twins continue working. They can contribute to long-term cost efficiency by optimizing the maintenance and operation of public infrastructure. By enabling predictive maintenance, digital twins can extend the lifespan of infrastructure and reduce the need for expensive repairs or replacements.
Digital transformation leads to better infrastructure projects
Ontario’s investment in digital twin technology is a forward-thinking move that demonstrates the potential of this technology to revolutionize public infrastructure projects. By enhancing risk mitigation, digital twin technology offers substantial benefits to governments, taxpayers, insurers and the construction industry alike.
For governments, digital twins are a powerful tool for managing infrastructure projects more effectively, ensuring that they are completed on time, within budget and in compliance with safety regulations. For taxpayers, this translates to more efficient use of public funds and improved infrastructure outcomes. Insurers benefit from more accurate risk assessments and streamlined claims processing, while those working in the construction industry enjoy a safer and more efficient work environment.
As digital twin technology continues to evolve and become more widely adopted, its role in the construction industry will expand even further—ushering in a new era of smarter, safer and more cost-effective public infrastructure projects.
Companies who make the investment in digitization will reap the benefits of building and operating a more resilient asset in the long term.
Elena Theodoropoulos is vice president and account executive for the North American Construction and Infrastructure Group at NFP, an AON company.
[This article appeared in the November/December 2024 issue of ReNew Canada.]
Featured image: The increasing use of digital twin technologies for public infrastructure projects is already changing how Canada’s insurance industry approaches the construction sector. (Getty Images)