By Vincent Davenport and Mark Gaglione
In the ever-evolving landscape of construction, a silent revolution is underway, and it goes by the name of mass timber. While wood has proven its worth as a building material over the centuries, mass timber is propelling it into a new era defined by sustainability, efficiency, and aesthetic appeal. As its popularity continues to soar, it becomes increasingly crucial to grasp the distinctions between building with mass timber versus traditional methods like concrete and steel. Additionally, uncovering the parallels existing within these materials can offer valuable insights, informing the construction process, and paving the way for successful mass timber projects.
Mass timber as a material and its procurement
While mass timber is fundamentally wood based, it’s essential to distinguish it from the light wood frame structures commonly seen in residential buildings. While light wood frame construction prevails, particularly in low-rise residential projects across Canada, the application of mass timber transcends these conventional methods. Mass timber projects stand out for their use of larger engineered wood products, adhering to rigorous engineering standards. Originating from sophisticated supply networks, these projects undergo meticulous engineering processes distinct from those governing light wood frame construction. Within the domain of mass timber, four primary types reign supreme: Cross Laminated Timber (CLT), Glue Laminated Timber (GLULAM), Nail Laminated Timber (NLT), and Dowel Laminated Timber (DLT).
Procuring mass timber products entails navigating a complex network of manufacturers and integrators. While some subcontractors specialize in producing mass timber products independently, others serve as integrators, sourcing components from various suppliers and overseeing the assembly process. Distinguishing between manufacturers and integrators is pivotal in formulating an effective procurement strategy tailored to the unique demands of a mass timber project. By delving into the intricacies of the supplier network and conducting a comprehensive assessment of factors such as equipment capabilities and expertise, contractors optimize their procurement processes, thus ensuring the success of their projects.
Building with mass timber
Mass timber boasts a distinct scheduling advantage, thanks to its prefabricated nature, which expedites on-site assembly. With pre-constructed beams and slabs ready for installation, mass timber follows a similar prefabrication process to structural steel and precast concrete, where off-site manufacturing and subsequent crane-assisted installation are standard practices. When comparing scheduling and installation analysis, mass timber aligns closely with precast concrete and structural steel, with crane efficiency being the primary determinant.
Similar to precast and steel structures, mass timber installations may not be entirely finished upon installation. There are often connections to be made or minor details to address once the main erection crew has departed. For instance, a concrete topping is frequently poured over the mass timber structure on each floor, mirroring practices seen in precast and steel construction.
Despite the perceived schedule benefits of mass timber, the reality may vary depending on the comparison made. Notably, significant schedule differences emerge when comparing mass timber to cast-in-place concrete. However, this comparison is akin to that between cast-in-place concrete and precast concrete or structural steel, highlighting the distinction between on-site construction and off-site prefabrication.
Another parallel can be drawn when we examine the integration of mechanical and electrical systems. Due to mass timber’s prefabricated nature, like precast concrete and structural steel, upfront coordination is essential for penetrations and openings to accommodate necessary piping and wiring.
A notable divergence in the building process compared to concrete or steel arises in moisture management. Wood’s vulnerability to moisture necessitates meticulous planning and proactive measures during construction. EllisDon has undertaken comprehensive studies to comprehend how mass timber behaves under diverse environmental conditions including dry, wet and very wet climates. This knowledge informs strategies we currently use on our projects across Canada, such as employing resistant membranes or adopting specific labour practices to address issues like puddling. These proactive steps mitigate moisture-related risks and safeguard the durability of mass timber structures.
Mass timber design and aesthetics
Before commencing a project, we conduct feasibility studies to assess the cost implications of constructing a mass timber building. Clients frequently approach us with existing concrete or steel structure plans, seeking insights using timber instead. Mass timber’s distinct material properties necessitate a re-evaluation of optimal grid layouts compared to conventional concrete structures. What may be an ideal grid for concrete might not be the most efficient for mass timber construction. Factors such as beam span and depth significantly influence design considerations, particularly regarding headroom requirements. For example, a beam comprised of mass timber can be two to three times as deep than a concrete beam that spans the same length. Adjustments to grid layouts are essential to optimize cost efficiency and structural integrity when working with mass timber.
In addition, the aesthetics of mass timber buildings offer a unique appeal and can be identified as a main factor behind the popularity of these types of structures. Diverging from the traditional look of concrete or steel structures, mass timber builds are characterized by exposed wood elements creating a distinctive atmosphere, often complemented by glass and steel accents contributing to a visually striking architectural style.
However, mass timber’s acoustic performance presents challenges compared to concrete. Its lighter weight inherently leads to poorer acoustic properties, requiring additional measures to achieve desired sound insulation levels. Strategies such as adding concrete toppings or acoustic membranes are employed to enhance acoustic performance while maintaining the exposed wood aesthetic. Addressing acoustic concerns involves strategic design decisions, including the addition of concrete layers or acoustic membranes to the mass timber structure. While solutions like drop ceilings or insulation can improve acoustics, they often conceal the visually appealing wood elements, presenting a design dilemma. As a result, the focus is primarily on enhancing acoustic performance from above while preserving the aesthetic appeal of exposed mass timber below.
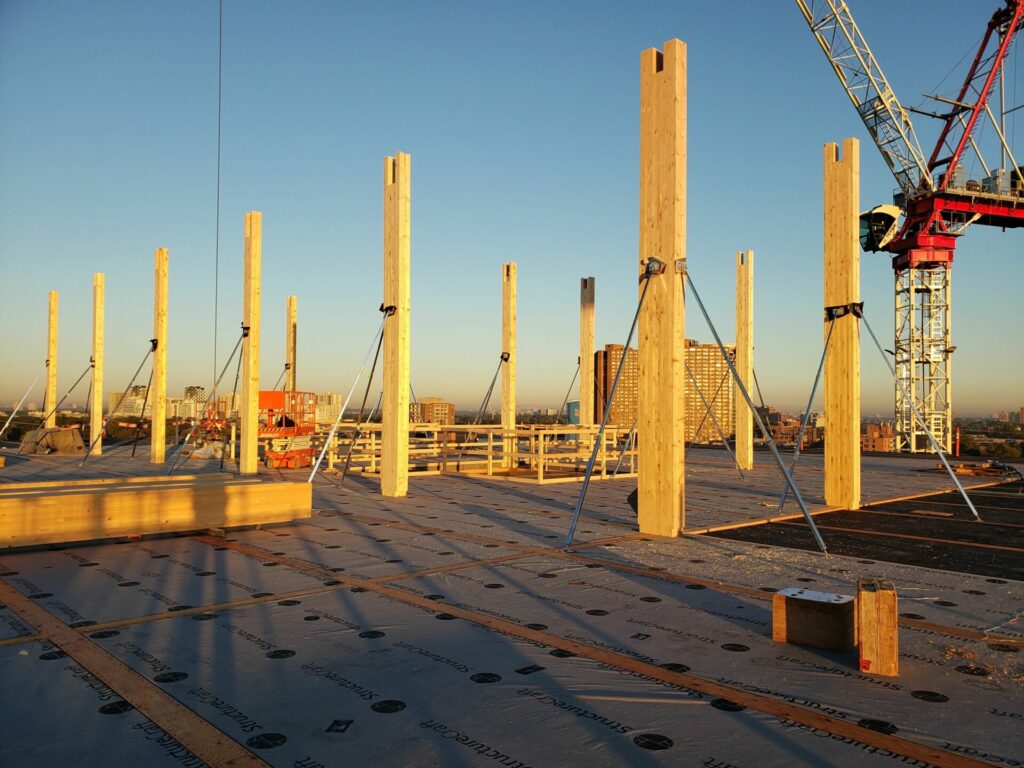
Building within and outside of code
The surge in mass timber discussions, not only at EllisDon but throughout the industry, can be attributed to significant shifts in the building code over the last decade. In 2015, the National Building Code expanded to allow for six-story buildings up to 18 metres,
followed by another pivotal change in 2020 introducing a new construction type, Encapsulated Mass Timber, allowing for structures up to 12 storeys. Alongside this, new requirements emerged, particularly regarding timber exposure, necessitating a minimum amount of covering to comply with fire safety regulations. This poses a challenge because with a mass timber structure, the aim is to celebrate the timber, not cover it up, prompting builders to explore noncompliant pathways or alternative solutions, which becomes more complicated.
Keeping up with demand
Despite the rapid evolution of the building code to accommodate larger mass timber structures with increased exposure, it often struggles to keep pace with market demands. Consequently, many projects end up navigating alternative solution pathways due to their complexity and deviation from standard code compliance. These alternative pathways for mass timber are different from that of a structure built with concrete or steel. Early engagement with a code consultant and subsequently, local building officials, is imperative to navigate mass timber’s intricate code landscape to identify compliant pathways for different building types.
While the code landscape with mass timber is more complex compared to conventional materials, it is improving. The next code change, currently being introduced, will allow for even taller mass timber buildings with even more exposure, signaling progress in the right direction.
Comparing the costs between mass timber, concrete, and steel structures reveals a nuanced picture. It’s not merely about swapping one material for another; rather, it involves considering various design elements and their associated costs. Factors such as acoustics and moisture management can increase the cost of building with mass timber, while some expenses can be offset within the interior. For instance, with exposed timber, fewer finishes are required, contributing to potential cost savings.
Overall, there’s still a premium associated with mass timber compared to traditional materials, but this gap has been narrowing over the past decade. Several factors contribute to this trend, including the decreasing cost of timber, growing familiarity with mass timber design and construction, and the emergence of more suppliers.
While costs related to constructing with mass timber are trending downward on average, insurance remains a significant challenge, with builders’ risk insurance premiums significantly higher compared to concrete and steel projects. Additionally, light wood frame and mass timber are insured in the same way, despite being very different products with distinct risk profiles. Despite this hurdle, efforts are being made within EllisDon by our team of insurance experts as well as throughout the industry to advocate for mass timber and educate insurance companies to mitigate this cost burden, fostering greater affordability and accessibility for mass timber construction.
Building with confidence
To effectively promote the adoption of mass timber as a construction technology, transparency is key. It’s essential to candidly discuss both its advantages and disadvantages when compared to traditional materials like structural steel and precast concrete. By openly addressing these factors, stakeholders can make well-informed decisions that drive the industry forward. Highlighting the similarities between mass timber and conventional materials not only eases clients’ concerns but also builds confidence in its efficacy. However, acknowledging the differences is equally important for a comprehensive understanding of each method’s strengths and weaknesses. This balanced approach fosters innovation and encourages sustainable and efficient construction practices, ultimately benefiting the industry in the long term.
Vincent Davenport and Mark Gaglione are Directors of Building & Material Sciences at EllisDon.
[This article originally appeared in the July/August 2024 edition of ReNew Canada]
Featured image: A beam comprised of mass timber can be two to three times as deep than a concrete beam that spans the same length. (Government of B.C.)