Technology is moving infrastructure projects forward.
By John Tenpenny
Technology is transforming the way Canadians do business. While the pace of change has accelerated and can be daunting, technology is making it easier for municipalities, engineers and constructors to design, build, operate and maintain the infrastructure assets we need for a robust economy.
Are there opportunities for greater use and faster adoption of technology? Are we taking advantage? Is our lack of knowledge, lack of capital, or a lack of willingness creating barriers to change?
During a recent INFRAIntelligence webinar, sponsored by Citylitics, ReNew Canada explored with experts in construction technology the use of technology in construction and public works, where it is being adopted and, perhaps more importantly, where it is not—and why.
E-permitting
One effect of the COVID-19 pandemic has been to drive more and more tasks online, from shopping for groceries to conducting meetings via technologies like Zoom.
The construction sector is no different. The push towards e-permitting has been going on for years, but that push has been ramped up over the past year.
A couple of years ago, the City of Windsor—the ninth largest municipality in Ontario—was the first municipality in Canada to go fully digital with its permit system.
John Revell, the city’s chief building official said the e-permit system put the city at the forefront when it comes to “offering a complete suite of online permit applications” that will allow builders to monitor the progress of their project through the online system using a tracking tool.
The technology chosen was from Finnish company Cloudpermit (formerly Evolta).
“When we started looking at going paperless we came across a lot of project management systems that were being reused for issuing permits and other things,” said Revell. “[This] product was customized specifically for the construction industry and we thought it might be a good opportunity to take us electronically to the next level.”
According to Richard Lyall, president of RESCON (Residential Construction Council of Ontario), “Ontario municipalities need a standardized development approvals process and streamlined e-permitting system to help reduce the amount of time it takes to get projects approved.”
Specifically, he pointed to the One Ontario proposal, which is requesting funds to establish guidelines for provincial data exchange standards for a comprehensive e-permitting system.
“That’s step No. 1,” he emphasized.
“We have over 20 organizations, including the planners, the building officials and the builders. What we’re saying is, ‘We want to do this. This is going to make things better. We need to have that data exchange capability for interoperability between systems and between jurisdictions.’”
According to Lyall, the World Bank ranks Ontario as 64th in construction permitting, and there are up to 45 agencies involved in the approvals process.
“If that process isn’t working smoothly, then you lose time, and if you lose time you lose money.”
Lyall said developers and investors must know when they’re going to get projects approved so they can figure out the numbers and measure risk.
“A very important part of this whole exercise is really de-risking the development process which is critical, especially with respect to any private sector-based investment.”
Ahmed Badruddin, CEO of Citylitics, a company that specializes in predictive intelligence of North American infrastructure markets, agreed.
“The trend of more digitization and data availability is skyrocketing in the public sector now that they need to provide services in a different manner. Generally, it starts with a clear goal: What do they want to do with the data? And a clear understanding of what kind of data they need. The best way is to start small and have some success before scaling it up.”
Digital Construction
We asked attendees some questions about the use of technology in construction. Here’s what they had to say:
What is the biggest barrier preventing technology adoption?
- Lack of knowledge 65%
- Lack of information 12%
- Fear of change 23%
How often do you use construction apps?
- 3-5 times per week 10%
- 1-2 times per week 15%
- Hardly ever 75%
It’s about the journey
Adoption is key and there are always early adopters, but what about the rest of the construction industry?
It usually starts at the highest levels, said Badruddin. “When we think about any transformative technology, it started with some public sector government application, which was then made available to the wider population.”
What Citylitics has found is that a lot of the data exists, but it’s not connected. “It’s in silos and from thousands of disparate sources and formats,” he said.
Where we saw an opportunity for technology was how do you use algorithms to pull all this data together so industry can make better decisions around what’s going on in the infrastructure market?
“Our approach is how do we make better use of the data that exists and leverage that, as a starting point. And then how do we find more data sources to plug into the system.”
Any change also requires a champion, said Revell, “because at the municipal level you’re working with a group of individuals who don’t all have the same understanding of what the benefits are and you’re competing against other priorities. It’s a matter of putting together a group of people who can advocate for it so that the political leadership is going to make the investment.”
It’s all about the journey, added Anna Robak, director, research and innovation with WSP Canada. “And part of it is how do we get industry to adopt technology, but part of it is internally, how do we get our own people to adopt these things?”
As infrastructure investment races to rebuild some of the economic damage from COVID-19, construction spending in Canada has taken centre stage. Our construction projects have long been a major investment industry—we spent $1.3 trillion on construction in 2019 alone, according to WSP research.
As part of a series called “Costing the Chasm,” WSP estimated that the costs of construction will rise significantly over the next 10 years due to 12 major trends the company identified, relating to areas such as climate, resources, society and technology.
“With more projects and greater expenses creating a double-edged challenge, left unchecked, construction costs could soar unsustainably high. But integrating smart technology throughout the construction lifecycle could play an important role in mitigating and even reversing those costs,” stated the report.
Something governments can do to help with technology adoption is support pilot projects, added Robak.
“There is nothing like a pilot project to get things moving.
“In the research I’ve seen on what makes people adopt something new, every single time, whether it’s purchasing a green product, allowing your private data to be used, every single time the person making the decision has looked at what someone else has done.”
A pilot project gives that first instance of somebody doing something and it being successful, or not, and the lessons that come from that.
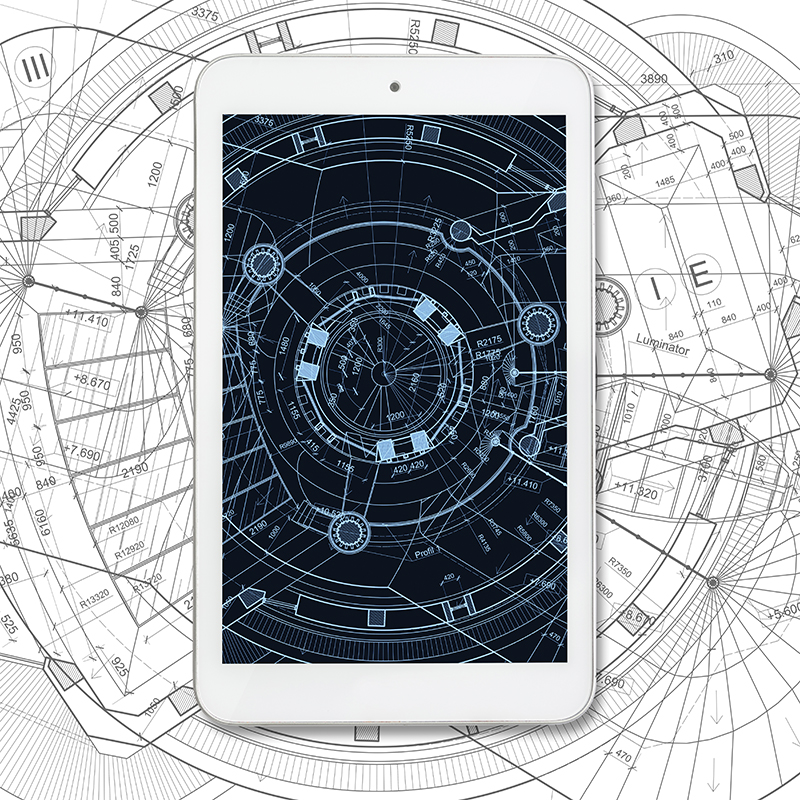
Benefits of technology
There are many real and potential benefits that can be derived from having digitized construction information, said Lyall, who pointed to a research project which looked at using drones and sensors where on any given day you have an up-to-date set of as-built drawings as the project is progressing.
While there are challenges, such as keeping up with the pace of change, Lyall said the future looks bright for the use of new technology in construction.
Drones and sensors can provide up-to-date information so drawings can be changed as a project is progressing, he said, and artificial intelligence (AI) can be used to simulate the effects of climate change on a structure so drawings can be revised to make it more energy efficient.
“And real-time location systems, using drones and sensors, can save up to 60 per cent of labour costs and cut construction timelines by 30 per cent.”
Robak agreed. “The benefits and the promise of data and the proper use of data is the capacity to simulate projects quickly and to change them and then run the apps on climate change issues. You can recalibrate the energy performance of buildings almost instantly.”
There are also practical benefits for the environment, added Lyall.
“We spend hundreds of millions of dollars every year reproducing drawings, many of which end up in a bin and never get used, which is really unnecessary.
In Windsor, Revell said they have already identified practical benefits that could save lives.
“We had an experience with our fire department. They were responding to a building fire and firefighters were sent into an underground space that was actually structurally compromised. Afterwards, the Fire Chief commented that he wished he had quick access to drawings of that building because he never would have put his firefighters in that part of the building had he known it was compromised.”
The situation speaks to having data accessibility, he added. “If this information is cloud-based then it’s something we can provide to the fire department and first responders can be looking at structural drawings on a tablet en route.”
It’s no longer science fiction
Artificial intelligence (AI) is another technology starting to find its way into the construction industry, according to Robak, who cited a recent study at the University of Waterloo.
AI gave researchers new insights to help reduce wear-and-tear injuries and boost the productivity of skilled construction workers.
Studies using motion sensors and AI software revealed expert bricklayers use previously unidentified techniques to limit the loads on their joints, knowledge that can be passed on to apprentices in training programs.
In their first study, the researchers analyzed data from bricklayers of various experience levels who wore sensor suits while building a wall with concrete blocks. The data showed experts put less stress on their bodies, but were able to do much more work.
“They’ve learned over the years how to move their bodies in a way that avoids injury or keeps them safe and healthy,” said Robak. “It’s something they wouldn’t be able to explain, but with cameras and AI they are able to monitor that movement and then train younger workers to move in a safer way.” The researchers are now developing a system that uses sensor suits to give trainees immediate feedback so they can modify their movements to reduce stress on their bodies.
“It’s a fascinating direct application to construction around keeping workers healthy, safe and more productive,” said Robak.
Looking ahead
Moving forward the architecture, engineering and construction (AEC) industries will encounter challenges.
One is that individuals in organizations making the decisions about the data are different from the ones using it and that can create adoption challenges, said Badruddin.
In today’s world many people are aware, they can’t ignore the data, they can’t ignore digital and they’re looking for smarter ways to use it.
Companies and organizations “need to keep the end user in mind. How is it going to improve their workflows?” said Badruddin. “You don’t want to overwhelm the user. You want to give them something simple, that is powerful, that enables them to do something they couldn’t easily do themselves before.”
Lyall said there is a disconnect because right now technology is evolving faster than our capability of keeping up with it.
“Necessity is going to drive change more than enlightened thinking because all of a sudden we’re going to realize that we’re 10 or 15 years behind some jurisdiction that we’re trying to compete with.”
He said there will be a big learning curve, because the reality is that not everyone is at the same level.
“Saying that you can accept applications by email is not e-permitting. Creating the platform to link different entities together so they can exchange and share data in a secure manner is critical.”
Robak said she finds it striking that every time WSP conducts a technology mapping exercise at a municipality, one department will not know about the technology another department has and the potential of that technology to grab data that will be useful to them.
“It’s very eye-opening,” she said. “There is potential for municipalities to use the technology they already have even better.”
There are some good models out there he commented, citing the example of the Eastern European country of Estonia’s digital identity model. Twenty years ago, the Estonian government made a commitment to digitally transform their society and now it’s estimated that 97 per cent of activity between the public and the government is online.
“When COVID-19 hit, they didn’t skip a beat,” said Lyall. “There is no reason we can’t do that.
It’s just a matter of time, effort, commitment and training.”
What the industry could really use is some kind of established cooperative venture involving government and industry and the design community to oversee the transition to increased use of technologies such as building information modeling (BIM).
According to the third annual BIM Report survey, conducted by the Building Innovation Research Centre at University of Toronto in collaboration with others, RESCON, “the use of innovative BIM-based processes and analyses can bring significant productivity improvements to the AEC industry. However, steps need to be taken to remove barriers that hinder a broader implementation. This report sheds light on those barriers, which include the need for an industry standard.”
The survey shows a progressive increase with respect to different entities at different levels of sophistication, said Lyall.
However, “there’s a push-pull effect. I’m not going to do it because the government doesn’t require it and government says I’m not going to ask them for this because they can’t do it.”
There are costs associated with change, but then there are benefits with the change that reduce costs, added Lyall.
Robak took a more aspirational view of the future.
“All organizations will have a policy of piloting, of trying out new technologies, of collaborating with each other, of gathering an evidence base so that they know what’s going to work and what’s not and then sharing that information.”
So, what does the future of construction look like?
“It will probably evolve in ways we haven’t even begun to imagine,” stated Revell.
John Tenpenny is the editor of ReNew Canada.