Cement Association of Canada CEO Adam Auer on the sustainable path forward
By Andrew Snook
This past Spring, the Cement Association of Canada (CAC) announced its Concrete Zero Action Plan for reducing Canada’s cement and concrete industry carbon emissions to net-zero by 2050. As part of this goal, a 40 per cent reduction in carbon emissions is the target for 2030.
To learn more about the CAC’s carbon reduction strategy for the cement and concrete industry, Renew Canada spoke to Adam Auer, CAC president and CEO. Auer joined the CAC in 2012, serving as vice-president of environment and sustainability, where he worked with government, industry, environmental and other civil society groups to promote and enhance concrete’s contribution to sustainability. Before joining the CAC, Auer managed Environment Canada’s Corporate Environmental Innovation initiative—a multi-stakeholder program to promote the business and financial case for corporate environmental leadership and the link between sustainability and an innovative and competitive economy. He has more than 20 years of experience in the field of sustainability.
Reducing the cement and concrete industry’s carbon emissions by 40 per cent by 2030 is a very ambitious target. What are the leading drivers for helping CAC members achieve this target?
We are focused on getting to net-zero by 2050, but we felt it was important to model what we think is achievable in a shorter timeframe as well. That’s why we included targets in our action plan for 2030 and 2040. And for 2030, it’s really an acceleration of existing emissions reduction strategies.
About 30 per cent of the emissions that are associated with the production of cement come from the combustion of fossil fuels. A big part of our strategy is to accelerate fuel substitution in our sector. We’ve overcome many of the policy barriers to be able to do that. And so, now we’re starting to see investments flow into the infrastructure to handle lower carbon fuels for facilities across the country, and significant reductions coming from that space within the 2030 timeframe.
The other big strategy is materials substitution by reducing the amount of clinker in our cements (clinker is the carbon intensive component of cement in the final cement recipe) and then making further reductions by using supplementary cementitious materials (SCMs) in the concrete that reduce the amount of cement, and effectively, the amount of clinker that ends up in your concrete.
In Canada, when we use supplementary cementitious materials, it tends to happen at the concrete phase. So, it’s integrated into the concrete mix design. But there are some further efficiencies, environmental and otherwise, by adding those same materials at the cement stage, grinding them with clinker, gypsum, and limestone, to produce a lower carbon cement. We already have some companies that have been introducing the use of those blended cements. We see an increase of that across the country as another part of our strategy to get to where we need to by 2030.
In the grand scheme of things, the biggest impacts will be after 2030. We see carbon capture utilization and storage (CCUS) as a big part of our net-zero action plan. Without CCUS, we estimate we can get over 60 per cent of the way to net-zero using a combination of strategies, like fuel substitution, clinker replacement and material efficiency in construction, but there’s no way to net-zero without CCUS.
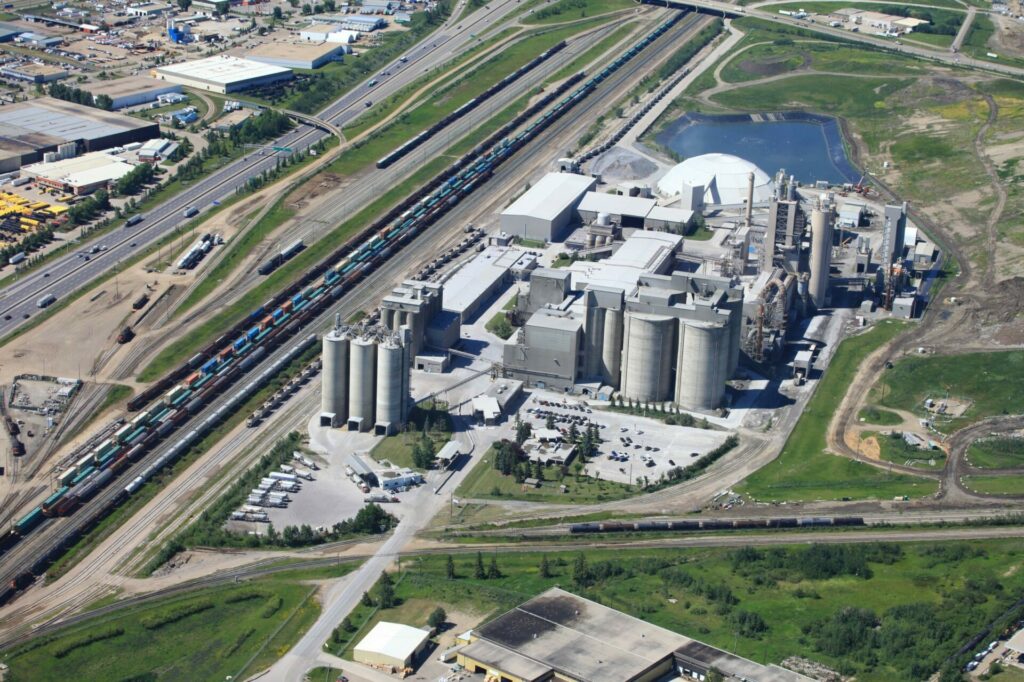
How big a role will the use of portland-limestone cement (PLC) play in the overall reduction of emissions for the industry?
This is an effort that we began well over a decade ago. It can replace up to 10 per cent of the clinker in cement and give up to a 10 per cent reduction in greenhouse gases associated with that cement.
When we look to 2030, we’re looking at finalizing our journey to full market penetration of that portland-limestone cement at the same time that we’re exploring PLCs that allow for even greater use of unprocessed limestone. Right now, PLC in Canada allows for a maximum of 15-per-cent limestone. But we know that we could increase that to 20 or 25 per cent. In some jurisdictions around the world this has already happened. So, we’ve begun the hard work around researching and testing those low-carbon cements to facilitate their introduction and adoption in the building code and lay the groundwork for market acceptance.
Can you describe the key technologies and alternative fuels/feedstocks that will be used to help the industry achieve these goals?
The amazing thing about cement and concrete is that its production process allows for recycling all sorts of different materials both as fuels and as material feedstocks for the kilns to make cement.
On the fuels side, looking at the 2030 timeframe, we’re really looking at the low-hanging fruit, which is capturing waste materials that have a calorific value, and that produce the heat signatures we need in our kilns to make cement. Our priority materials are biomass feeds because these are considered carbon-neutral fuels. For example, construction and demolition waste is primarily biomass—a lot of wood waste. But we can also use agricultural waste. We can also use non-recyclable tires, or the residue from tire recycling; non-recyclable plastics; and even municipal solid waste and sewage sludge. These are all materials that can be used as lower carbon replacements for fossil fuels like coal and petcoke.
What barriers exist for companies using alternative fuel sources?
The previous barrier was that the policy environment around permitting for fuels and cement kilns didn’t really allow for alternatives outside of traditional fossil fuels in many jurisdictions across the country. And so, we have had to work with provincial governments to create an environmental compliance assessment regime and permitting regime that recognizes the environmental benefits of those alternative fuels. And I would say this barrier has largely been overcome. And so now, the challenge is effectively establishing the supplier relationships to find the feedstocks and have them processed either externally, or on site, to make them compatible with the cement manufacturing process. This is something that some of our members in Canada have a lot of experience with from operations around the world. In Europe, they are close to 60-per-cent fuel substitution on average now, and they certainly have some plants that are 100-per-cent substitution.
In Canada, where we do need more in terms of investment in R&D and commercial scaling of alternative fuel technologies is in the beneficiated biomass space—biochar, biocoal, and other future fuels like green hydrogen. These are all fuels that could play a greater role in cement manufacturing and help further reduce emissions after 2030. But right now, there isn’t really a lot of supply, and what supply exists is prohibitively expensive. So, there do remain some barriers when we look beyond 2030.
What role do you see carbon capture utilization and storage technologies and projects playing in assisting the industry in its emissions targets?
Carbon capture utilization and storage (CCUS) technologies are needed because of those industrial process emissions. About 30 per cent of our emissions are coming from combustion, and about 60 per cent of the emissions come from the sintering of the limestone in the kiln. Limestone is calcium carbonate, and that carbon is released in the heating process. That’s what allows for the chemical reaction to take place to make clinker. And so those emissions are effectively irreducible, and that’s why CCUS becomes essential. It’s really the only technology that exists today to mitigate the process emissions from the calcination of limestone in the kiln.
There are two cement facilities in Alberta where there’s already a pretty mature conversation about CCUS technologies. Of course, Alberta already has the CO2 transportation infrastructure. They also have significant identified geologic storage space, and they have the regulatory and liability regimes more-or-less sorted out. So, it’s quite advanced in terms of providing that fertile field of regulatory and infrastructure resources that are needed to support CCUS. The Heidelberg Materials facility in Edmonton, and the Lafarge Canada facility in Exshaw are actively pursuing carbon capture utilization and storage, with the aim of producing net-zero cement by 2030, or as early as 2026 in the case of Heidelberg’s Edmonton plant.
What else can be done to help the industry meet its goal of net-zero carbon emissions by 2050?
In our action plan we really look across the whole value chain. We call it the five C’s: clinker, cement, concrete, construction, and carbonation. We really wanted to be able to articulate within each of those C’s who we need to partner with to remove obstacles or to create the right incentives and environment for these solutions to succeed in the market. We are transparent about what we are doing, and planning to do, and what we can do on our own on the industrial manufacturing side.
We also clearly articulate how the construction industry needs to work with us on things like optimizing mix design, and figuring out how we can integrate material efficiency into the design of our structures. How do we need to change construction practices and design practices to be able to incentivize those types of solutions?
In many ways this is a call to action to our partners in the construction value chain, as well as government, to work with us to make reductions that are achievable with today’s technology; and to work with us to make sure the regulatory and market environment are aligned with the goal of reducing carbon and bringing those solutions into the market. We can’t do it alone. These things are not possible just by the cement sector and concrete sector acting independently. We need partnerships to be successful.
Andrew Snook is a freelance writer based in Mississauga, Ont.
[This article originally appeared in the November/December 2023 edition of ReNew Canada]
Featured image: Adam Auer has been with the Cement Association of Canada since 2012 and was appointed president and CEO in 2022.